|
[Ĩ¸¶¿îÅÍ] 392V 385 µ¿Àϱâ´É ÀÛ¾÷¹üÀ§ ³ÐÀ½
 |
HOME > Products > SMD Pick & Place
SMD Pick & Place
|
|
|
|
»óǰ¸í |
[Ĩ¸¶¿îÅÍ] 392V 385 µ¿Àϱâ´É ÀÛ¾÷¹üÀ§ ³ÐÀ½
|
|
|
Á¦Á¶»ç |
Autotronik-SMT |
|
|
|
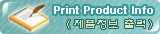 |
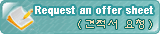 |
|
|
|
|
|
|
|
|
|
DETAILS
Strong and rigid mechanical
design
BA392
using welded steel frame and also heavy duty high precision Linear Ball Rail
system to provide strong, rigid and long life time
mechanism. |
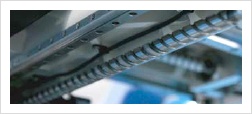
|
High-Precision, Direct-Drive, allscrew and Linear
Encoder Technology BA392 base system features
high-precision, direct-drive ballscrew and linear encoder technology in the X
and Y axes, contributing to its 30 µm, 3 Sigma placement
accuracy. |
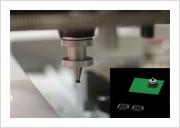 |
COGNEX¢ç Alignment System "Vision on the
Fly"
The
BA392 features COGNEX¢ç vision processing and head-mounted for non-contact
¡°Vision on the Fly¡± alignment. The machine BA392 assures high-precision
placement of the full range of SMDs, from the smallest 0201 devices through
CSPs, µBGAs, flip-chips, ultra-finepitch QFPs (0.3mm fine pitch), even odd-form
components. |
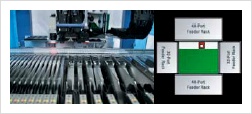
|
Extensive Placement
Area BA392 with stand-alone
configurations has maximum 650 mm x 350 mm of payload area can be shared by PCBs
and waffle trays. Placement area increases to 660 mm x 330 mm for in-line
setting. |
Feeder Rack Included in delivery are 2 x FR-48K, each is suitable
for 48 x 8mm KFTA Feeders or 40 x 8mm IC-Sticks. 2 x FR32K can also be mounted
on the left and right sides of the machine for a total capacity of 160 8 mm tape
feeders.
|
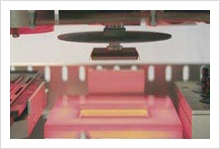 |
Bottom
Vision Alignment System(Option) A Bottom Vision Camera is
used for large components up to 150 x 100 mm and devices with alignment features
on their bottom side. |
Smart Fiducial System Beside the standard fiducial mark, either square SMD
PCB pad or plate-through hole also can be trained as fiducial mark. For more
precise placement of fine pitch components, additional Local fiducial
recognition is provided. |
Universal CAD Conversion
Beside the direct input of data by teach-in
camera, an optional CAD conversion program is available for directly transfer of
CAD generated pick and place data. |
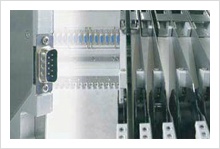 |
Auto Tape Feeder (KFTA) The innovative design of KFTA feeder bases and
mounting hardware allows almost limitless flexibility in feeder combinations and
arrangement schemes, as almost every feeder can be ordered, loaded, programmed
and mounted independently. KFTAs are available from 8 mm up to 72 mm tape
width. |
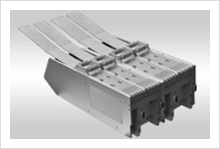 |
Universal IC Tube Feeder KFTB universal tube feeder are using vibration driven
technique. It is able to handle IC-Sticks with max.50 mm
width. |
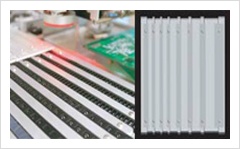 |
Cut Strip Tape Holders (Short tape Staion) Cut Strip Tape Holders is a handy accessory for
present-ing components that are supplied in short lenghts of tape due to their
low quantity of usage. It can also prevent the waste of components in sections
of tape that are too short to be loaded into tape
feeders. |
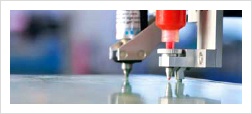
|
Dispenser System Optional stand alone dispenser head for adhesive
& solder paste dispensing. Perfect for quick, small volume production
without making stencil. |
Conveyor System
The already
included conveyor system with SMEMA Interface and motor-driven-width-control
speeds up the handling of PCB and in-line
production. |
LED application In respond to the increased use and variety of
surface mount LEDs application, BA392 has the upgrade capacity for LED
application. |
Bulk Pack Component Tray Designed for bulk pack component, Bulk Pack Component
Tray (TSD18) can handle any bulk pack component under the semi-auto production
mode. A single tray contains 18 individual slots for maximum 18 types of
components. |
IC Tray Holder The standard TS-1 Tray Holder occupies approximately
330mm X 140mm of work area and is designed to hold a standard 316mm X 136mm
JEDEC Matrix Tray. The TS-1 provides adjustability for wide variety of smaller
matrix tray and waffle pack combinations and can easily be modified for custom
tray configurations. |
Tray Handler System Optional IC tray handler system can access up to 10
sets of waffle Trays automatically. |
Buffering Nozzle
The spring buffering design of Nozzle adjust
the placement pressure for different heights of components
automatically
|
Vision Inspection With the built-in software, the camera can
automatically move and display the image in the computer screen. User can
manually check the printing accuracy of solder paste, quality of the soldering,
accuracy of component placement, etc |
Remote Service
Kit
Optional Remote Service Kit allows a remote
access to machine by Internet, so that programming, calibration and service can
be done by our worldwide remote service
center. |
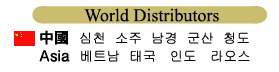

| |
|
|
|
|
¡¡ |
SUMMARY |
¡¡ |
• Large 600 mm x 350 mm placement area
• Suitable for 160 intelligent Auto Tape Feeder
• High Accuracy and high Flexibility for 01005, 0201, 0402, 0603,
SOIC, PLCC, BGA, ¥ìBGA, CSP, QFP, up to fine-pitch 0.3mm
• Smart Feeder System provides Automatic feeder position checking
• Automatic component counting, Production data Traceability
• Perfect for small & medium volume production
• COGNEX¢ç Alignment System ¡°Vision on the Fly¡±
• Bottom Vision Alignment System for fine pitch QFP & BGA
• Built in Camera System with Auto Smart Fiducial Mark Learning
• Dispenser system
• Vision Inspection before and after production
• Windows XP Software
• Universal CAD Conversion
• Placement rate: 6,400 cph
• Tray Handler access up to 10 Waffle Trays
|
• AUTOTRONIK BA392 features high-precision, direct-drive ball screw and linear encoder technology in the X and Y axes, contributing to its 30 µm, 3 Sigma placement accuracy. With high-power AC servo motors allowing placement rates approaching 6400 cph.
• With feeder bases on all four sides, BA392 has maximum 8mm smart type feeder capacity of 160, and 600 mm x 350 mm of payload area can be shared by PCBs and waffle trays. Placement area increases to 630 mm x 350 mm with feeder bases mounted on only the front and rear of the system and an in-line conveyor installed.BA392 with stand-alone or In/Out conveyor configuration is suitable for any In-Line or "Work Cell" manufacturing environment.
• The head-mounted, upward-aimed cameras with Cognex¢ç vision processing and programmable illumination of BA392 allow easy set-up for a wide range of SMDs,including odd form components and BGAs.Base mounted cameras with a wider optical range and diagonal split-vision image processing can even be used for alignment of large components up to 150 mm x 100 mm.
|
|
|
|
|
¡¡ |
Model |
¡¡ |
BA392V |
¡¡ |
No. of heads (Vision on Fly) |
¡¡ |
2 |
¡¡ |
Placement rate (uner the optimum condition) |
¡¡ |
6400 CPH(Under the optimum condition 5500 CPH(IPC 9850 Chip 1608) |
¡¡ |
Feeding capacity (8mm) |
¡¡ |
up to 160 Tape Feeders (without conveyor) up to 96 Tape Feeders (with conveyor) |
¡¡ |
IC Tray capacity |
¡¡ |
up to 4 Waffle Trays up to 10 Waffle Trays with TH-10 Tray (option) |
¡¡ |
Component Size (mm) |
¡¡ |
Handled by head camera -Smallest : 0.6 x 0.3 mm -Largest : 16 x 14 mm Handled by fixed Bottom Vision camera -Smallest : 0.4 x 0.2 mm (option) -Largest : 150 x 100 mm (option) |
¡¡ |
Resolution |
¡¡ |
X-Y Axis 0.005 mm Servo Motor Z Axis 0.02 mm Servo Motor |
¡¡ |
Radiation |
¡¡ |
0 to 360¢ª (0.045¢ª/step) Servo Motor |
¡¡ |
Placement Accuracy |
¡¡ |
+/- 0.03 mm |
¡¡ |
X-Y Repeatability |
¡¡ |
+/- 0.01 mm |
¡¡ |
Place Area |
¡¡ |
Placement area without conveyor Max. 600 x 350 mm without Waffle Trays Max. 600 x 330 mm with 1 Waffle Tray Max. 600 x 190 mm with 2 Waffle Trays
Placement area with conveyor: Max. 650 x 315 mm without Waffle Trays Max. 650 x 300 mm with 1 Waffle Tray Max. 650 x 160 mm with 2 Waffle Trays |
¡¡ |
Programming |
¡¡ |
- Direct input - Vision teach-in - CAD Access (Option) |
¡¡ |
Component Sense |
¡¡ |
Vision detection |
¡¡ |
Main Control |
¡¡ |
Industrial PC |
¡¡ |
Machine Size (Main body) |
¡¡ |
1150 x 1100 x 1350 mm (L x W x H) |
¡¡ |
Weight |
¡¡ |
550 kg |
¡¡ |
Power |
¡¡ |
230 V / AC 2100W |
¡¡ |
Pressure |
¡¡ |
75 psi (5.5 bar) |
|
|
|
|
|
• Non-contact Linear Encoder System (option) By using "Closed Loop" Servo Motors with non-contact Linear Encoder System, provide extremely high Repeat-ability and Stability.
• Bottom Vision Alignment System (Option) A Bottom Vision Camera is used for large components up to 150 x 100 mm and devices with alignment features on their bottom side. Due to additional Bottom Vision Camera, the alignment of 01005 components is guaranteed.
• Universal CAD Conversion Beside the direct input of data by teach-in camera, an optional CAD conversion program is available for directly transfer of CAD generated pick and place data.
• Conveyor System The optional conveyor system with SMEMA Interface and motor-driven-width-control speeds up the handling of PCB and in-line production.
• Handled by fixed Bottom Vision camera (Largest) -Smallest : 0.4 x 0.2 mm (option) -Largest : 150 x 100 mm (option)
• Placement Accuracy
+/- 0.03 mm (by optional linear encoder)
|
|
|
|
|
|